top of page

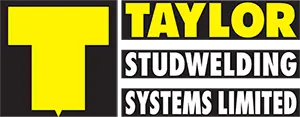
+44 (0) 1924 452123
sales@taylor-studwelding.com
RESOURCES
Stud Welding FAQs
Here are some frequently asked questions that our team at Taylor Studwelding get asked. Use this information to find out more about the stud welding process, our products and customer service.
bottom of page