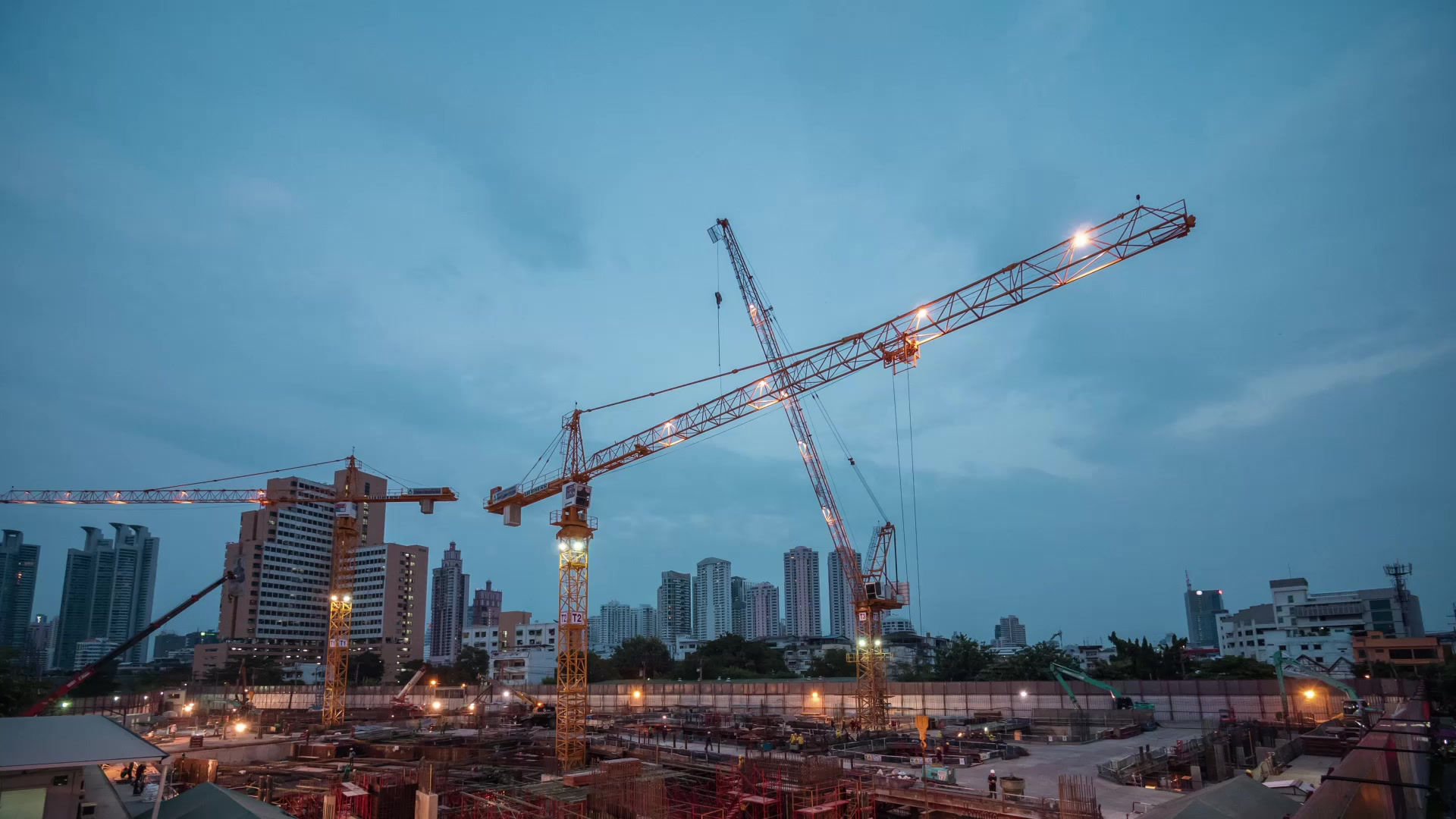

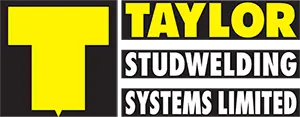
+44 (0) 1924 452123
sales@taylor-studwelding.com
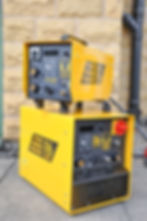
At Taylor Studwelding we are committed to continuous R&D and investment into new equipment design to retain our title as the UK’s leading stud welding equipment manufacturer. When it comes to stud welding technology, precision, efficiency, and cost-effectiveness are key factors in selecting the right equipment. At Taylor Studwelding Systems, we are leading the industry with our advanced range of drawn arc (i12 and i16) and capacitor discharge (CDi) stud welding equipment, all featuring state-of-the-art inverter/switch mode transformer technology. Compared to traditional transformer rectifier designs, this cutting-edge approach offers numerous advantages across both welding methods, making it the superior choice for modern manufacturing and construction applications.
High-Frequency Inverters: Faster Adjustments, Consistent Performance
The use of high-frequency inverters in Taylor Studwelding’s i12 and i16 drawn arc models enables ultra-fast response times, which is a game-changer in stud welding. Unlike traditional transformer rectifiers, which can lag in adjusting to dynamic welding conditions, our inverter technology allows for rapid and real-time control over the weld parameters. This ensures that each weld receives the exact energy input required - minimising material distortion and reducing spatter for cleaner, stronger welds every time.
Reduced Material and Manufacturing Costs
A major drawback of conventional transformer rectifier designs is their reliance on large amounts of copper. With the ever-increasing costs of copper, these traditional systems are becoming more expensive to manufacture and maintain. Inverter-based systems, however, utilise much smaller transformers, significantly reducing material costs without compromising performance. This applies to both our drawn arc and CDi capacitor discharge ranges, resulting in more affordable, efficient welding solutions that offer long-term savings for businesses.
Lightweight and Portable: A Game-Changer for Site Work
Another key advantage of inverter technology is its compact and lightweight design. Traditional stud welding equipment is often bulky and requires mechanical handling for transportation and setup. However, Taylor Studwelding’s inverter-based systems are lightweight enough to be lifted and positioned by just one or two people. This makes them ideal for on-site applications where mobility is crucial, reducing setup time, increasing efficiency, and improving safety for operators.
Inverter vs. Transformer Rectifier Welders: A Clear Advantage
While inverter-based welders provide numerous benefits, it is important to understand how they compare with traditional transformer rectifier systems:
Precise Control & Fast Response – High-frequency switching allows for real-time adjustments, ensuring a stable and consistent welding current across both drawn arc and capacitor discharge methods.
Energy Efficiency – Uses significantly less power compared to traditional transformer rectifiers, reducing electricity costs.
Lightweight & Portable – Inverter welders are much smaller and easier to transport, often operable by one or two people.
Reduced Copper Usage – Requires smaller transformers, lowering material and manufacturing costs.
Cleaner Welds with Less Spatter – More stable arc results in minimal material distortion and reduced post-weld cleanup.
Higher Duty Cycle – Can run longer without overheating compared to traditional transformer-based welders.
Leading the Way in Advanced Stud Welding Technology
At Taylor Studwelding Systems, we are proud to push the boundaries of what’s possible in stud welding. Our inverter-based drawn arc (i12 and i16) and capacitor discharge (CDi) welding systems provide unmatched control, efficiency, and cost-effectiveness, making them the go-to choice for industries that demand precision and reliability. Our welding machines also contain other features that are emerging trends, shaping the future of stud welding. Our latest range includes user-friendly interfaces redefining operator experience, data collection for smarter welding and eco-conscious design.
Switching to inverter technology is not just an upgrade—it’s a strategic investment in the future of stud welding. Contact us today to learn more about how our 40 years in innovative stud welding manufacturing can elevate your welding operations.