

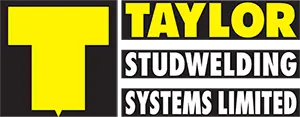
+44 (0) 1924 452123
sales@taylor-studwelding.com

What is Studwelding?Â
In short, stud welding is a method of applying a single side fastening to a metal component. It is a time honoured process that has been used since the early 1900’s and is highly versatile in terms of its applications.
This article explores the typical problems experienced with other fixing and fastening methods and how Stud Welding can be a highly effective alternative process for many applications. We’ll look at examples of where Stud welding is often the most appropriate or best solution.Â
The Problems – Fixing & Fastening
Drilling & Tapping
These fastening processes are very slow; a thicker parent material and longer studs are required.

Inserts
Inserts can eventually work loose, plus they crack paint and leave unsightly stains. Holes need to be punched and deburred in parent material, weakening it. The reverse side is not always clean and flat.

Back Welding
This process is slow and requires weakening the parent material from punching and deburring holes. The excess weld needs grinding off for a clean flat finish.

Through Bolting
Through bolting requires two handed assembly and access from both sides. Bolt heads are unsightly and stains can come from the bolt holes. The assembly is not leakproof and the parent material is weakened by the presence of holes.

The Solution – Stud Welding
The benefits of using a stud welding system include fast attachment with no reverse marking. The welded joint is stronger than the parent material or the stud and access is only required from one side. No holes are made, hence no leaking or weakening of the sheet. Tamperproof, pre-coated or painted materials can be welded. The equipment is portable and easily jigged; in fact, stud welding overcomes all of the disadvantages of the aforementioned processes.

What Is Stud Welding Used For?
Stud welding is a highly versatile process for attaching fastenings to metal sheets. Using weld studs, operators can automatically or manually form welds of superior strength. As a result, there are many stud welding applications available. Using stud welding to attach weld studs is a faster and more efficient process for attaching fasteners. You can use a range of stud welding processes to achieve strong attachments on a variety of metals; this makes it a great welding system for many industrial applications.
Stud Welding Applications
With 40+ years of development and experience, Taylor Studwelding Systems designs its products with a wide range of uses in mind. From mechanical manufacturing to electrical equipment, stud welders are useful for a wide selection of sectors. Find out more about the diverse range of industries and areas that benefit from the selection of stud welding applications technologically available on the market today:
Automotive
Stud welding is a highly valued and indispensable technique within the automotive industry. This is because accuracy and strength are of paramount importance in welding fastenings to sheet metals. Automotive manufacturers can use stud weld equipment for diverse automotive applications. Examples include:
Exhaust Systems – Stud welding ensures a secure attachment of flanges and brackets, allowing for efficient exhaust gas flow and minimising the risk of leaks or dislodgement.
Heat shields – These are effectively mounted using stud welding, providing critical protection against excessive heat and safeguarding surrounding components from potential damage.
Power Steering – Stud welding contributes to the stable attachment of brackets and support structures, ensuring smooth and reliable steering performance.
Insulation – The fastening process is used to securely connect insulating materials, preventing heat transfer and enhancing overall energy efficiency.
Electrical Wire Routing – This is a vital aspect of modern automotive systems. Wire harnesses and cable management components are firmly secured through the precision and strength of stud welding, minimising the risk of electrical malfunctions and simplifying maintenance and repairs.
Automotive Lighting – Stud welding also plays a significant role in this application, enabling secure mounting of lighting fixtures onto the vehicle’s body. This not only ensures proper alignment and visibility but also enhances the vehicle’s appearance.
Stud welding’s ability to create strong and long-lasting connections whilst eliminating the need for additional fasteners or intrusive welding methods makes it a winning process in automotive manufacturing. The wide range of stud welding equipment available, allows for streamlined and efficient manufacturing processes, reducing production time and costs for automotive manufacturers.
Construction
The superior strength and reliability of stud welds makes this welding process highly suitable for a wide range of construction applications. Across the construction industry, stud welding is harnessed for various projects, including building work, bridge construction, and more. Underground systems, such as sewer pipes and other subsurface utilities, also require strong welding for safer buildings and roads. Examples of how stud welding is used across these areas of construction includes:
Building Work – Stud welding finds widespread use in fastening steel beams, columns, and other load-bearing elements. This creates robust connections, enhancing the overall stability and structural integrity of buildings, whether they are skyscrapers, commercial complexes, or residential structures. Stud welding equipment also proves instrumental in attaching metal cladding panels, roofing systems, and facades, resulting in secure weather-resistant exteriors that contribute to the aesthetics of buildings
Bridge Construction – These construction projects often involve challenging environmental conditions and demanding engineering requirements. Bridge building projects benefit greatly from stud welding’s capabilities. Studs are skillfully welded onto bridge components, such as girders, expansion joints, and deck plates, providing a secure link that can withstand heavy loads, dynamic forces, and the effects of exposure to the elements. This enhances the overall safety and durability of the bridges, ensuring their reliability for years to come.
Underground Systems – These are a crucial element of modern day infrastructure and the strength of stud welding is an equally essential part of this. Sewer pipes and subsurface utilities require solid welding to ensure secure, water tight connections that minimises the risk of leaks, structural failures, or hazardous situations are eradicated. The reliability of stud welds contributes to the creation of safer underground infrastructure, including sewer lines, water supply networks, and electrical conduits, which are essential for the proper functioning of cities and urban areas.
Road Construction – The durability of structures is vital and therefore stud welding is applied in areas such as highway barriers, guardrails, and road signs. These elements require secure attachments to withstand impacts from traffic and provide crucial safety measures for drivers and pedestrians.Â
The widespread use of stud welding in construction applications is a testament to its exceptional strength, versatility, and reliability. Whether in towering skyscrapers, imposing bridges, underground utilities, or vital road infrastructure, stud welding continues to be an indispensable tool, providing the necessary strength and security for building a better and safer world.
Catering and Food Processing
Stud welding is ideal for fastening applications where hygiene is paramount, such as items in the catering and food processing industries. These sectors demand strict adherence to cleanliness standards to ensure the safety and quality of food products. The stud welding process leaves no gaps or dirt traps around the bases of the welded studs meaning that there is nothing that could compromise food safety.
In catering settings, stud welding is utilised to fasten various elements to tabletops and counters. These could include equipment stands, preparation stations, and serving areas. By securely attaching these fixtures with stud welding, the risk of dislodgement or contamination due to loose components is significantly reduced, ensuring a safe and efficient food service environment.
Stud welding is also employed to fasten essential equipment, such as refrigeration units and food processing machinery, to prevent any potential hazards or hazards associated with loose equipment. These sturdy attachments not only ensure a smoother workflow but also facilitate easier cleaning processes by eliminating gaps or recesses where debris or pathogens could accumulate.
In environments where electrical items are used for food processing or catering, stud welding is instrumental in securing electrical enclosures and components. The reliable and airtight connections created through stud welding prevent the infiltration of contaminants or moisture, safeguarding the electrical equipment’s functionality and preventing any potential safety risks.
Stud welding’s ability to create flush and seamless connections is a crucial advantage in these industries. Unlike conventional fastening methods, stud welding leaves no gaps or irregularities around the bases of the welded studs. This allows working areas to be easily cleaned when they might otherwise have been hard to disinfect thoroughly. The absence of such hard-to-reach areas enhances the overall hygiene standards.
CladdingÂ
Building Cladding is a construction technique that refers to adding components to the outside of a building. Stud welding finds significant application in building cladding work, where it is employed to securely attach metal cladding panels to building structures. Cladding is used to provide thermal insulation, fireproofing, weather resistance and for improving building aesthetics.Â
Stud welding offers a robust and efficient method for fastening metal cladding materials, such as aluminium, stainless steel, or galvanised steel, to the underlying support structure. During the process, metal studs are welded to the building’s framework or wall surface, creating a series of anchoring points. The cladding panels are then simply attached to these studs using various techniques, such as sliding the panels onto the studs or using mechanical clips. Stud welding ensures a strong and lasting connection between the cladding and the building, with no visible fasteners on the cladding surface, resulting in a clean and sleek appearance.Â
This method is widely preferred in cladding work due to its speed, cost-effectiveness, and ability to handle a wide range of materials, making it an ideal choice for both commercial and residential buildings.
Decorative and Consumer Items
The invisible nature of stud welding results makes it perfect for decorative and consumer items and the fastenings can be found in many everyday items. This unique characteristic allows for fastenings that are not only strong and durable but also aesthetically pleasing, enhancing the overall appeal and quality of the products. Various industries benefit from the advantages of stud welding in producing an array of items, including jewellery, badges, cookware, homeware, and more.
In the realm of cookware, stud welding finds widespread application in the assembly of pots and pans. The hidden welds create a smooth and elegant exterior, devoid of visible fasteners, which not only enhances the visual appeal but also ensures a hygienic surface that is easy to clean. Stud welding plays a vital role in attaching handles to cookware like saucepans and kettles, guaranteeing a secure, leak-proof and long-lasting connection, essential for the safe and reliable handling of hot pots and pans.
Stud welding is also used for doors, particularly in the case of escutcheon plates and insulation, offering a discreet and robust method for affixing components. These hidden welds ensure a neat and uncluttered appearance, contributing to the door’s overall aesthetics without compromising its functionality and insulation properties. In commercial doors, stud welding allows for the secure attachment of various hardware and fixtures without visible screws or bolts, creating a sleek and professional look.
Stud welding can be applied for intricate uses too. Badges, emblems, and jewellery benefit from stud welding’s ability to create strong connections without any visible marks or deformities. In the case of badges and emblems, this method ensures a flush and sleek appearance. Stud welding also plays a vital role in jewellery assembly, securing delicate pieces without compromising their aesthetics or structural integrity.
Electrical
Stud welding is perfectly suited to the intricate fastening processes needed for electrical items encompassing various applications across different industries. Its versatility and precision make it well-suited for securing components in motors, communication equipment, electrical homeware, and a wide array of electronic systems.Â
Motors – stud welding plays a vital role in mounting various parts, such as endplates and brackets, with robust connections. The secure attachment of these components ensures the motors’ efficient functioning and longevity, critical for a wide range of industrial and consumer applications.
Communication equipment –  stud welding is instrumental in fixing fascia panels and other critical elements, providing a clean and sleek appearance while maintaining the necessary structural integrity. This is especially crucial for telecommunications devices, routers, and networking equipment.
Electrical homeware – stud welding facilitates the assembly of items like microwave ovens, refrigerators, and washing machines, ensuring secure and stable fastenings of internal components. This enhances the appliances’ reliability and safety, meeting the high standards expected by consumers.
Electronic Systems – systems such as those used in automation, data transmission, and test equipment, stud welding allows for precise and efficient mounting of printed circuit boards (PCBs). The welds ensure a stable connection for the delicate electronic components, minimising the risk of vibration-related issues and optimising the overall performance of these systems.
Earthing Studs – stud welding serves an essential role in fixing earthing studs, which are vital for grounding electrical equipment to prevent electrical hazards and ensure a safe working environment.
Small Electrical Items – Mounting smaller items like switches and buttons in various electrical devices and control panels is made easier and more aesthetically appealing with stud welding, as the fastenings are neat and unobtrusive.
Hydraulic Lines & Electrical Enclosures – drawn arc stud welding is particularly suitable for applications in these areas. The process ensures strong and leak-resistant connections, crucial for efficient fluid transmission and protecting sensitive electrical components from external elements.
Electrical Control & Security Equipment – across a wide range of industries, stud welding is extensively employed in the assembly of control and security equipment, medical instruments, lighting fixtures, domestic appliances, power generation, and distribution systems. In each of these applications, the precision and strength of stud welding contribute to the reliable performance and extended lifespan of the electrical items.
Stud welding continues to play a crucial role in enhancing the efficiency, reliability, and safety of electrical devices and systems in the modern world.
Farming and Agriculture
Various pieces of farming and agricultural equipment are manufactured using a stud welder. The versatility of stud welding enables equipment companies to manufacture and fasten a wide range of components including:
Brackets are an integral part of farming equipment, providing support and stability for various attachments and implements. Stud welding allows these brackets to be securely fixed to the main framework of the equipment, ensuring the components stay in place during demanding tasks such as ploughing, harvesting, and tilling.
Cabs, the enclosed cabins where the operator sits, require a strong and secure connection to the equipment’s body. Stud welding is instrumental in attaching the cabs, providing a safe and comfortable environment for the operators while also offering protection from external elements and hazards.
Fenders are crucial components in agricultural machinery, shielding the equipment and surrounding area from debris and crop residues. Stud welding ensures the fenders are firmly attached, even in high-impact conditions, safeguarding both the equipment and the personnel working nearby.
Spreader machines used for fertilising and seeding rely on precise and robust fastenings to distribute materials effectively. Stud welding plays a significant role in assembling spreaders, providing durable connections for smooth and efficient spreading operations.
Thresher teeth are essential in harvesting machinery, requiring a strong attachment to handle the pressure and forces involved in the harvesting process. Stud welding ensures these teeth are securely mounted, preventing any issues during harvesting and reducing downtime due to maintenance or repair.
Shrouding, which includes protective covers and shields, is crucial for safety and performance in agricultural equipment. Stud welding enables equipment companies to attach shrouding securely, offering protection from moving parts and hazards, thereby enhancing the overall safety of the machinery.
Hose and wiring management within the agricultural industry is benefited by stud weld fastenings too. Fastening hoses securely prevents leaks and reduces the risk of damage during operation. Similarly, managing wiring with stud welding ensures that electrical systems remain organised and protected from wear and tear, leading to more reliable and efficient equipment.
Furniture
Stud welding is widely used in the furniture production industry. Furniture assembled using a stud welder includes desks, filing cabinets, shelving, racks, and additionally garden furniture for the office or home.
Stud welding allows for furniture to withstand the weight of items such as computers or documents and enables furniture such as shelving units to eliminate the risk of structural failure. It also allows for aesthetically pleasing design of furniture for the home or office environment, removing the need for visible screws or bolts providing a clean and professional appearance.Â
In terms of garden furniture, including patio chairs, tables, and benches, secure fastenings are required to withstand outdoor elements such as rain, wind, and sun exposure. Stud welding ensures that garden furniture remains stable and durable, even under harsh weather conditions, providing comfort and longevity to users.
The fastening process offers a rapid and efficient assembly process, contributing to increased productivity in furniture manufacturing. The fast welding process allows for shorter production cycles and faster turnaround times, enabling manufacturers to meet market demands effectively.
Green Energies
Stud welding is a widely used fastening process in the green energy industry, particularly in the construction and maintenance of wind farms and other renewable energy resources. The versatility and reliability of stud welding make it an ideal method for various applications within these sustainable energy sectors, contributing to the efficient and long-lasting operation of renewable energy systems.
Wind Farms – stud welding is employed extensively during the construction of wind turbine towers. The tower sections are often made of steel and require precise and robust connections to ensure structural integrity and stability. Stud welding allows for secure attachment of flanges, brackets, and other components, providing a strong and reliable assembly process. The tower’s strength and durability are crucial for withstanding the continuous forces and stresses imposed by wind currents, ensuring the safety and longevity of the wind turbines.
Wind Turbine Blades – Stud welding is also used in wind turbine blade construction. The blades need to be aerodynamically efficient and capable of withstanding extreme weather conditions. Stud welding is used to fix brackets, root sections, and reinforcements onto the blade structure, creating a smooth and seamless surface that enhances aerodynamic performance. The strong and concealed connections provided by stud welding contribute to the overall efficiency of the wind turbine.
Solar Energy – stud welding finds applications in other renewable energy resources, such as solar energy. Solar panel mounting structures, made of steel or aluminium, require secure attachments to support the panels and ensure proper orientation towards the sun. Stud welding allows for rapid and reliable fastening of the mounting brackets, making solar panel installations more efficient and durable.
Hydroelectric Power Plants – stud welding is essential in the construction of hydroelectric power plants and geothermal energy systems. In hydroelectric power plants, stud welding is used to attach components in water turbines, such as blades and guide vanes, enabling efficient energy generation from flowing water. In geothermal energy systems, where high-temperature and corrosive environments are common, stud welding provides durable and resistant connections for critical components.
Biomass & Bioenergy Facilities – Stud welding is used in the construction of biomass boilers and biofuel storage systems. These installations require the fastenings to handle the high temperatures and harsh conditions associated with biomass combustion and storage. Stud welding ensures that the boilers and storage structures can withstand these challenges, contributing to the reliability of the entire biomass energy process.
Heating and Ventilation
Stud welding is a highly valuable technique within this industry. It is ideal for fixing insulation materials and pipes. Operators also use stud welding to fix burners and heating elements, mount fluid chambers, and attach items such as flanges, hatches, and covers. It helps to ensure efficient temperature regulation and minimise heat loss in both heating and cooling systems.Â
Stud welding is instrumental in boilers and heating systems as it provides strong and stable connections ensuring that crucial components are securely mounted, guaranteeing effective heat generation and distribution in both domestic and industrial boilers. Stud welding also offers a precise attachment of components which is ideal for mounting valves, pressure sensors and other fittings with accuracy, ensuring optimal flow of proper operation of the system. Stud welding’s leak-proof fastenings is a big benefit for this use too.
Stud welding is widely used in domestic and industrial air conditioning and ventilation units. It is applied to fix critical components, such as compressors, fans, and condenser units. These components must be firmly mounted to ensure efficient operation, and stud welding provides the necessary strength and stability required.Â
In refrigeration systems, stud welding is used to attach components such as evaporators, condensers, and refrigerant lines. The airtight and reliable connections achieved through stud welding again contribute to the overall efficiency and cooling performance of the refrigeration systems, whether in commercial or residential settings.
Industrial
Even the most complex industrial machinery manufacturing can benefit from stud welding. Big manufacturing companies use Taylor Studwelding equipment for attaching machinery guards, fixing cover plates and maintenance hatches, mounting handles, and also fixing air/fluid lines.
Machinery Guards – an essential component in ensuring operator safety and protecting the machinery’s moving parts. Stud welding allows for the secure and precise fixation of these guards, providing a robust barrier against potential hazards and reducing the risk of accidents or injuries in the workplace.
Fixing Cover Plates and Maintenance Hatches – these plates and hatches provide access points for maintenance and repairs, and their secure attachment is vital for efficient servicing without disrupting the equipment’s operation. Stud welding enables the integration of these components, ensuring easy access for maintenance personnel while maintaining the machinery’s structural integrity.
Mounting handles – this is essential for ease of operation and manoeuvrability. Stud welding ensures that handles are firmly attached, capable of withstanding the stresses and forces associated with machine operation. The reliable connection provided by stud welding ensures that handles remain in place, preventing any potential risks or difficulties in handling the machinery.
Fixing Air and Fluid Lines in industrial machinery – Air and fluid lines are required for the proper functioning of hydraulic, pneumatic, and cooling systems in various machinery. The secure attachment provided by stud welding ensures that these lines are leak-proof and properly positioned, preventing any potential disruptions to the machinery’s performance and optimising efficiency.
Stud welding contributes to the overall speed and precision of industrial machinery manufacturing. The rapid welding process allows for faster assembly times and reduces production cycles. The strength and durability of welding connections also make it the preferred choice for industrial machinery that operates in challenging and demanding environments, whether that be heavy-duty manufacturing processes, construction sites, or mining operations as it can withstand rigorous conditions prolonging its lifespan and reducing maintenance costs.Â
Insulation
Stud welding is a fast and reliable method for securing insulation materials to metal surfaces in HVAC systems, industrial boilers, shipbuilding, and construction. By welding insulation pins or studs directly onto metal, insulation blankets, panels, and wraps can be firmly attached without drilling or adhesives. This ensures long-term durability, improved energy efficiency, and reduced labour time. Whether for thermal, acoustic, or fireproofing insulation, stud welding provides a strong and permanent hold, making it the go-to solution for insulation attachment in demanding environments.
Mechanical
In the mechanical industry, stud welding finds applications across various sectors. From material handling and conveyors to lifts, metal furniture, transportation, construction, and general machinery, stud welding plays a crucial role in ensuring secure and robust connections that withstand the demanding environments and heavy-duty operations.
Material handling and conveyors are essential components in industrial processes, enabling the efficient movement of goods and materials. Stud welding is employed to attach brackets, support structures, and guiding elements in conveyors, ensuring smooth and reliable material flow. The strong and durable connections achieved through stud welding contribute to the overall productivity of material handling systems, reducing downtime and maintenance needs.
Lifts, whether used in commercial buildings, warehouses, or transportation vehicles, require precise and reliable fastenings for safety and functionality. Stud welding enables the secure attachment of lift components, including rails, guide brackets, and support structures, ensuring smooth and safe vertical movement for passengers and cargo.
Metal furniture, known for its strength and durability, also benefits from stud welding’s reliable fastening solutions. Stud welding allows for seamless and hidden connections in metal furniture, enhancing its aesthetics and structural integrity.Â
In the transportation sector, stud welding is employed in various applications, including securing brackets and components in vehicles, trailers, and aircraft. In commercial and industrial trucks, stud welding facilitates the attachment of cargo restraints, securing items during transport and ensuring safe deliveries. For rail transport, stud welding is used in the assembly of railway tracks and components, offering durable and long-lasting connections capable of withstanding heavy loads and constant wear.
Construction machinery relies on stud welding for strong and reliable attachments in heavy equipment such as bulldozers, excavators, and cranes. The sturdy connections provided by stud welding contribute to the equipment’s structural integrity and stability during demanding construction operations.
General machinery in industrial settings, such as manufacturing plants and factories, benefits from the versatility of stud welding. Whether in the assembly of robotic arms, automation systems, or process machinery, stud welding enables efficient and secure fastenings, contributing to the smooth and precise functioning of the machinery.
Medical EquipmentÂ
Stud welding is widely used in the medical industry for various applications that require secure and precise connections. The versatility of the welding technology makes it a valuable tool in medical equipment manufacturing, contributing to the development of high-quality and safe medical devices.
One of the primary uses of stud welding in the medical industry is in the assembly of medical carts and trolleys. These carts are required for transporting medical equipment, supplies, and medications within healthcare facilities. Stud welding enables the attachment of shelves, drawers, and accessories to the cart’s frame, ensuring secure and durable connections that can withstand the frequent movement and handling of medical equipment.
In medical equipment manufacturing, stud welding is employed to fix components in various devices, including diagnostic equipment, surgical instruments, and imaging machines. The precise and reliable fastenings provided by stud welding allow for the proper alignment and stability of critical components, optimising the accuracy and performance of medical devices.
Stud welding is also instrumental in the production of hospital beds and patient care equipment. By securely attaching side rails, lifting mechanisms, and other components, stud welding ensures that these devices can support patients safely and comfortably, meeting the rigorous standards of the medical industry.
In medical furniture manufacturing, stud welding is applied for fixing brackets, handles, and other accessories on items such as examination tables, treatment chairs, and IV stands. The sturdy connections created through stud welding enhance the durability of the medical furniture, catering to the specific needs of healthcare facilities.
Stud welding is also applied in the construction of medical imaging and radiation therapy equipment. These devices require precise and stable positioning of various components, such as gantries, collimators, and detectors. The process ensures that these critical components remain securely attached, maximising the accuracy and safety of medical procedures.
The hygienic advantages of stud welding are also significant in the medical industry, particularly in devices used in sterile environments. Stud welding creates smooth and seamless connections, reducing the risk of dirt traps or crevices that could harbour bacteria or contaminants.Â
Shipbuilding
Stud welding is a widely used joining process within the industry that addresses various construction and assembly needs. The rapid and reliable attachment of fasteners onto metal surfaces along with its durable and strong bond means that it is very often a preferred or essential fastening process. Shipbuilding companies use stud welding machines for various applications including:
Wire and Cable Management – In modern ships, there is an extensive network of electrical wires and cables that need to be securely routed and managed. Stud welding allows shipbuilders to affix cable hangers and supports onto bulkheads and decks, ensuring organised cable pathways and reducing the risk of damage during operation or maintenance.
Fluid Lines – Ships require complex fluid systems for fuel, water, air, and other liquids. Stud welding facilitates the attachment of pipe hangers and brackets, providing stable support for fluid lines throughout the vessel. This ensures a safe and efficient distribution of fluids, essential for smooth operation at sea.
Control Panels and Electrical Systems – Stud welding is instrumental in the installation of control panels and various electrical components onboard. Mounting these systems with stud welding ensures their firm fixation, which is crucial for the reliable functioning of critical shipboard equipment.
Hatch Covers – Proper sealing of hatch covers is essential for a ship’s integrity and buoyancy. Stud welding allows shipbuilders to secure gaskets and sealing elements on hatch covers, maintaining water-tightness and protecting cargo from exposure to seawater.
Insulation – Ships require insulation to regulate temperature and prevent heat transfer. Stud welding is employed to fasten metal brackets and supports for insulation materials, ensuring they remain securely in place even under harsh marine conditions.
Decking – Ships’ decks endure considerable stress and load-bearing requirements. Stud welding is used to attach structural elements and deck fittings, enhancing the overall strength and stability of the vessel.
Hull Construction – In some cases, stud welding is also used in hull construction, where metal plates and components need to be securely joined to form the ship’s main structure. The process ensures strong connections while maintaining the integrity of the hull.Â
The advantages of using stud welding in shipbuilding are numerous. The fast and efficient jointing method significantly reduces assembly time and labour costs. The resulting connections are durable, with excellent resistance to vibrations, making them ideal for the dynamic environment of the open sea. Stud welding is a non-intrusive process, minimising the risk of damage to the parent materials during the attachment.
Signs and Lettering
Stud welding is extensively used in the sign-making industry to quickly and effectively affix signs and lettering. With the aid of a stud welding gun or an automated CNC system, sign makers can securely attach signs and lettering to various surfaces, regardless of their size or intricacy. This process is particularly advantageous when dealing with large-scale sign installations, ensuring a strong and lasting connection between the signage and the mounting surface.
Sign makers use the stud welding process for a broad range of applications. This includes outdoor signage for businesses, public spaces, and events, where durability and weather resistance are paramount. Stud welding provides a hidden fastening method, contributing to the clean and professional appearance of the signs, even in harsh outdoor conditions.
In the interior design realm, stud welding is applied to decorative panels, nameplates, and signs. Whether it’s in commercial spaces, retail environments, or residential settings, hidden welds ensure a refined and elegant finish, adding to the overall aesthetic appeal of the interior design elements.
Stud welding is also used as an ideal solution for mounting signs and lettering on uneven or irregular surfaces. The process can securely attach signage to materials like concrete, stone, or brick, providing a reliable and sturdy attachment that withstands the challenges of different substrates.
The use of stud welding is not limited to large-scale signs and installations. It also caters to smaller, intricate lettering and detailing in various applications, such as creating bespoke nameplates, plaques, and memorial signs. It is also used to create 3D lettering and signage too. The precision and accuracy of stud welding ensure that intricate details are affixed securely, contributing to the overall quality and craftsmanship of the signage. The process of capacitor discharge stud welding is particularly beneficial when dealing with thin sheet materials like steel, aluminium, and brass. Tip ignition is the most cost-effective solution for welding these materials, offering a reliable and precise method for affixing lettering and signage to delicate surfaces.
This fixing method is often a preferred choice in the sign-making industry due to its speed and efficiency. The rapid welding process enables sign makers to meet tight production deadlines and handle high-volume orders with ease.
The sheer range of stud welding applications doesn’t stop there! To see if stud welding is the right process for your operations and for advice on which systems and processes are best, get in touch with Taylor Studwelding today and we will be more than happy to advise you.