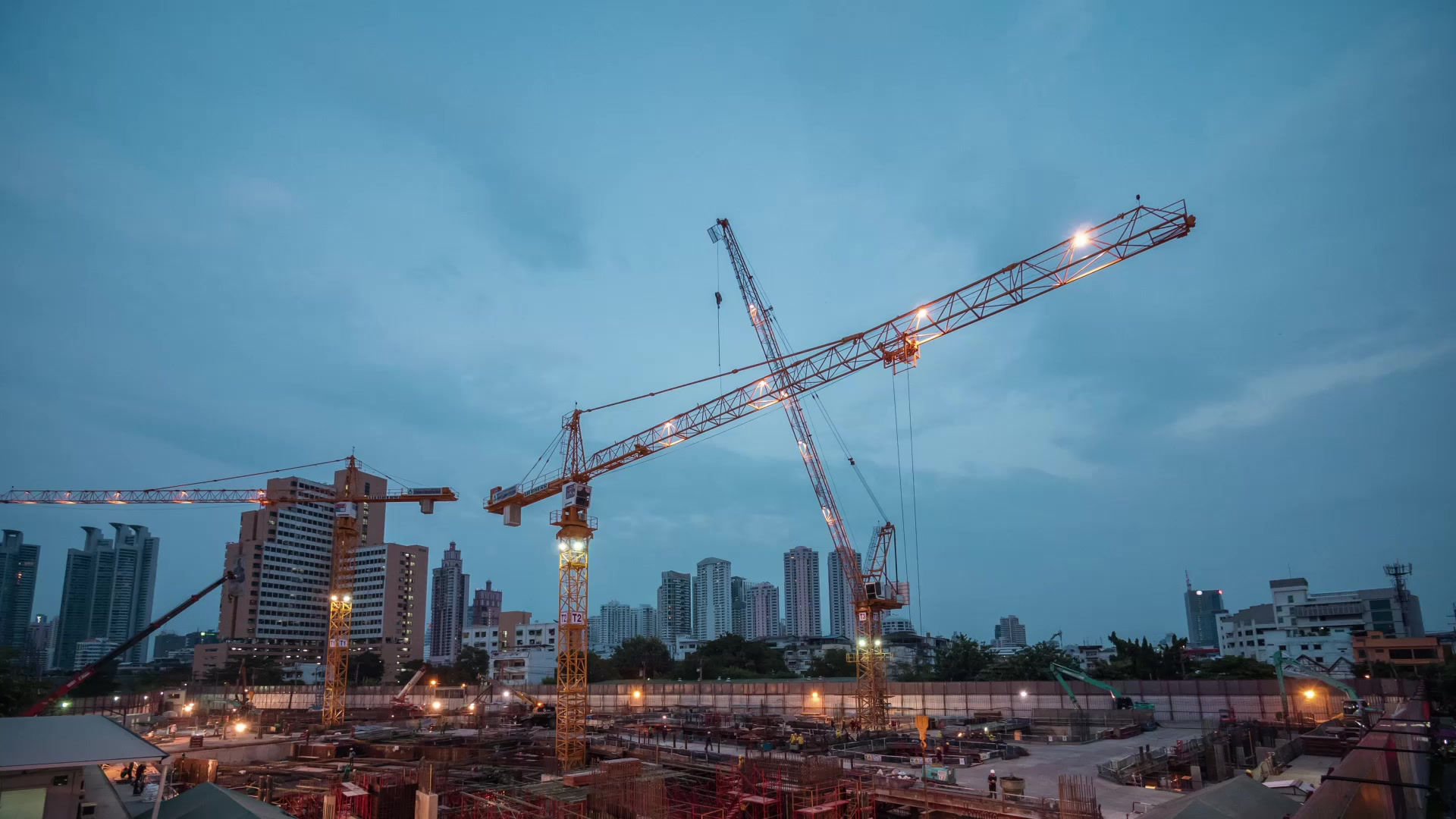

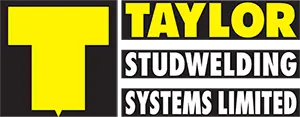
+44 (0) 1924 452123
sales@taylor-studwelding.com

Sustainability is a huge topic in the manufacturing industry today, with high levels of importance being placed on the priority to preserve our planet. There is a common desire across the globe to help to improve the environmental impact that businesses have on the world with a goal of reducing emissions of greenhouse gases whilst also removing emissions from the atmosphere. The UK government has set targets for companies to achieve net zero by 2050.Â
Sustainability is a top priority for Taylor Studwelding as a manufacturer of equipment that plays a pivotal role in the supply chain for many industries. Here are some of the things that we are doing to maximise sustainability when manufacturing stud welding machines and accessories.
Minimising Material Waste – We have very minimal material waste from the manufacture of our equipment. All the components needed for assembly are purchased as required and do not have a shelf life so they can be stored if needed and ensure that there is no wastage.Â
Environmentally Accredited Supply Chain – We use a supply chain for components that are verified for their environmental accreditations.Â
Certified with ISO 14001:2015 – Taylor Studwelding holds up-to-date accreditations for environmental management, currently certified with ISO 14001:2015. This means that our customers can be assured that we have robust processes in place ensuring environmental responsibility such as adequate recycling facilities, disposing of trade waste etc.Â
Minimising Energy Usage – Taylor Studwelding pays great attention to energy usage as an essential way to minimise our environmental impact. We have policies in place to ensure that power and electricity is not overused.
Omitting Harmful Substances – Every product that Taylor Studwelding produces does not contain any substance that is classified as harmful. We ensure that everything supplied by us does not contain any substances governed by REACH or RoHS.
Minimising Emissions – Throughout the whole production line, Taylor Studwelding actively minimises emissions. Additionally, we minimise travel requirements offering online demonstrations and video tutorials to save on travel emissions.
Use of Electric Vehicles – The business has invested in electric vehicles for business travel so that any essential travel uses vehicles that have a minimal impact on the environment.
Research and Development – We are constantly investing in research and development to enhance the efficiency of the stud welding machinery that we produce. For example, following client feedback we are adding new features to our products to display how much energy is being used. This allows users to get a power consumption reading from their machine usage. We are currently developing a cloud solution to feed energy consumption data from the welding process automatically, fully recording data ready to be analysed by the client.Â
Sustainability and managing our environmental impact remains top of our agenda at Taylor Studwelding. We will continue to look for new ways to minimise our environmental impact during the manufacturing process, doing our bit to help achieve a sustainable planet.